Business
How to Optimize the Performance of Pneumatic Cylinders in High-Speed Operations
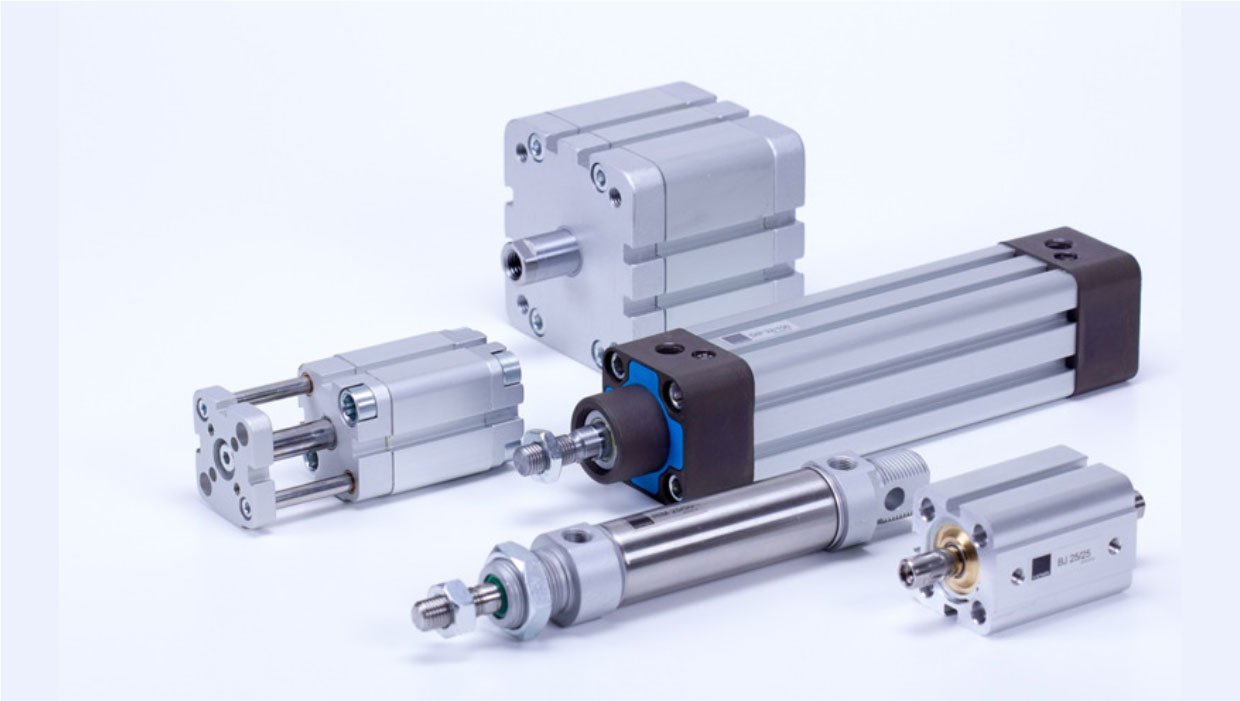
In such a rapidly growing environment like industrial automation, the functionality of the pneumatic cylinders during high-frequency operation is of paramount importance for continuous productivity, safety of the personnel and a reduction in overall life-cycle costs. Pneumatic cylinders are widely used in automation systems as the key elements that define the productivity and quality of the processes used in manufacturing. Based on this case study, this article will discuss some proven solutions to increase performance of pneumatic cylinders in high speed applications to help the firms in industrial automation systems companies.
Understanding Pneumatic Cylinder Performance
Pneumatic cylinders function by adapting pneumatic energy as a force for production, generally for moving mechanical components of machines, for instance conveyors, robotic arms, and presses for use in production lines. Therefore, the efficiency of these cylinders on high speed trims relies on aspects such as size, pressure, and controls of the airflow. These parameters must be managed to guarantee that pneumatic cylinders will not only be capable to accommodate the high speed requirements but will not affect the performance and durability of the material.
As much as designing a pneumatic cylinder for precise application, it is crucial to know how a pneumatic system works within the industrial environment. A pneumatic system where one transfers the air in a reservoir and directs through the cylinder using valves to produce force. They are used to turn a piston that creates either; LINEAR movements/ ROTARY movements. To increase the performance it is imperative that the whole of the pneumatic system be optimized to have low leakage of air, correct pressure and right components..
Proper Sizing for High-Speed Applications
As will be discussed below there are various aspects that need to be considered when using a pneumatic cylinder in high speed operations, but perhaps the most important of them is the size of the cylinder to be used. Naturally, pneumatic cylinders are available in different sizes and stroke lengths and if the wrong size is selected, it will result in slow movement, low efficiency or the cylinder pulling itself apart.
The industrial automation systems companies are in effect required to calculate the actual force required for their operations in terms of the load weight, required speed and the stroke length. By choosing cylinders with proper bore and Stroke length, the companies can guarantee that its pneumatic system is powerful enough to augment a particular task but not too powerful to overdo the task.
Adjusting Air Pressure for Optimal Speed
Performance of pneumatic cylinders is greatly influenced by air pressure. Insufficient pressure leads to slow movement or jerky movements and on the other extreme a higher pressure could reduce the life cycle of the cylinders and other parts of the system. It is important to regulate the air pressure at operational optimum in order to project the car to achieve its optimal performance.
Proportions and force should also be maintained in pneumatic cylinders through appropriate pressure levels. There are always specific requirements in the operation of industrial automation systems, that is why companies use regulators to adjust the pressure to the desired level. Also, amperes must also have a strong compressor to keep steady pressure for the cylinders so that smooth operations of parts in higher speeds is achieved.
Minimizing Air Leakage and Friction
Using high speed application with pneumatic cylinders causes two major challenges that is air leakage and friction. A small amount of leaking can cause pressure drop which in result cuts the energy velocity of the system. On a similar note, leakages in another commonly used equipment, the pneumatic cylinders, and its corresponding attachable part including the seals and valves, can also be spotted from regular maintenance as well as inspection.
Another influence that/contributes to/reduces the performance of the cylinders is friction. In order to reduce some of these effects, companies in industrial automation systems can consider using high quality seals, bearings and lubricants. Additional layers of polymers can be deposited on the piston rod of the cylinder in order to offer minimum frictional forces for additional enhanced functionality. When these strategies are incorporated into the design of the system, the system will operate more fluidly and provide faster response in high speed applications.
Implementing Advanced Control Systems
For a pneumatic cylinder to perform efficiently high-speed motion control applications requires the integration of intelligent control systems that are capable of measuring and controlling pressure, position of the cylinder as well as the velocity. These systems can further be set up in a way that the individual parameters are changed dynamically so that the cylinders are most optimal throughout the process.
Proportional valves and other controllers, for instance, enable flow control based on sensor information, and provide some control over velocity and position of the cylinder. It’s an added advantage where fast operations have to be performed with precision and quick response in equal measures. Thus, applicants of industrial automation systems can incorporate these systems into their machinery to guarantee that the corresponding pneumatic cylinders for their operation offer the needed speed and precision.
Routine Maintenance and Monitoring
However, it is advocated that high frequency rates require pneumatic cylinders to be generously sized, well pressurized, and exceptionally controlled, maybe in intervals regular maintenance is crucial for them to last in high speed work. The cylinders, valves, filters, and any other parts used are subjected to normal wear and tear; general check ups will enable the early detection of probable problems which are likely to cause breakdowns or require expensive repairs.
Every company is therefore encouraged to come up with a maintenance schedule that includes the inspection of air leaks, filter cleaning and replacement, oiling of any mechanical parts and checking of pressure levels. Furthermore, condition monitoring systems can also improve specific cylinder data in real-time for cylinders performance and identify cylinder performance depreciation as early as possible.
Enhancing pneumatic cylinders in high-speed applications involves a strategic approach to engineering, semantics, and maintenance in the system. Industrial automation systems companies can ensure that their pneumatic cylinders are performing at their best by choosing the right cylinder size and checking the air pressure, fixing leaks and reducing friction and implementing high end control systems. These enhance production rates, system efficiency and effectiveness and, hence economical in the current market focus of industrial institutions.
For More Information Visit Loopermagazine
-
Celebrity9 months ago
Who Is Jordan Broad?: The Untold Story of Ashley Broad Husband
-
Celebrity9 months ago
Who Is Mary Ryan Ravenel?: Inside The Life Of Thomas Ravenel’s Ex-Wife
-
Celebrity9 months ago
Who Is Noelle Inguagiato?: The Untold Story Of Jesse Watters Ex-Wife
-
Celebrity9 months ago
Who Is Dolphia Parker?: Everything About Dan Blocker’s Wife